The production process of small-sized copper flat wire is indeed more complicated than that of conventional copper wire, and the technical requirements involved are more stringent. This is because small-sized copper flat wire has very high standards in terms of size, shape, strength, conductivity and ductility. The following are the technical requirements and process controls that need special attention in the production of small-sized copper flat wire:
1. High-precision rolling process
- Precision rolling technology:Since the width-to-thickness ratio of small-sized copper flat wire is very high, precision rolling technology is required during the production process to ensure that it meets precise requirements in thickness, width and surface finish. Usually, precision rolling requires the use of equipment such as a four-roll mill, UC6-roll mill or 20-roll mill to ensure the quality of the copper flat wire.
- The difference between cold rolling and hot rolling:Cold rolling is often used in the production of small-sized copper flat wires, which can improve the strength and dimensional stability of the copper flat wires. However, during the cold rolling process, the material will be subjected to greater stress, so the temperature, pressure and speed during the rolling process need to be precisely controlled to avoid cracks or deformation.
2. Strict temperature control and annealing process
- Annealing control:Since the thickness of small-sized copper flat wire is relatively thin, the annealing process is particularly critical. Annealing can not only improve the plasticity and ductility of the copper wire, but also eliminate the internal stress caused by rolling. The annealing temperature and time need to be precisely controlled to avoid oxidation of the copper wire surface or degradation of performance.
- Temperature uniformity of annealing furnace:Uneven temperature may cause inconsistent hardness in some areas of the copper flat wire, affecting its performance. Therefore, the temperature in the furnace must be uniform during the annealing process, and the annealing time must be accurately adjusted according to the specifications of the copper wire.
3. Cleaning and surface treatment
- Cleaning technology:Small-sized copper flat wires require extremely high surface finish, and any impurities or contaminants may affect their electrical properties and appearance. Therefore, after the rolling and annealing process, strict cleaning must be carried out. Common cleaning methods include the use of degreasing agents, pickling and passivation. Each stage of cleaning must ensure that there is no oil or oxide residue.
- Surface passivation: The surface of the copper wire needs to be passivated after pickling to form a protective film to prevent oxidation of the copper wire surface and maintain its good conductivity.
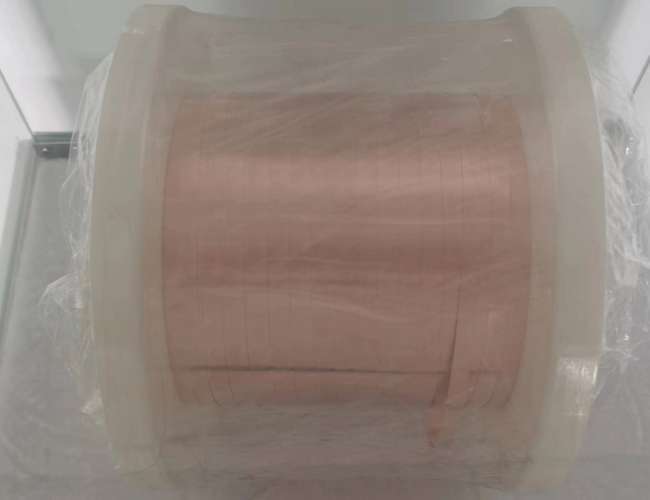
4. Requirements for copper materials
- High purity copper:Small-sized copper flat wires have very high requirements for material purity. The higher the purity of the copper material, the better its conductivity, ductility and corrosion resistance. Commonly used copper materials include high-purity oxygen-free copper (Cu-OF), which has fewer impurities and can effectively improve the conductivity and mechanical properties of copper wires.
- Alloy copper wire: In some special applications, copper alloys (such as copper-nickel alloy) may be used to make copper flat wire. This alloy copper wire has stronger corrosion resistance and oxidation resistance, and is suitable for small-gauge copper flat wires used in harsh environments.
5. Controlling the elongation and hardness of small-gauge copper flat wire
- Tensile properties:The tensile properties of small-gauge copper flat wires must be strictly controlled to ensure that they will not break during use. Usually, the tensile strength and elongation of small-gauge copper flat wires need to meet certain standards, especially in applications that require bending or deformation.
- Balance of hardness and toughness:Small-gauge copper flat wires need to find the best balance between hardness and toughness. Too hard copper wires may cause brittle cracks, while too soft copper wires may not be able to withstand the required mechanical stress. Therefore, the hardness needs to be precisely controlled during the production process to achieve appropriate ductility and strength.
6. Finished product testing and quality control
- Dimensional accuracy:The dimensional accuracy of small-sized copper flat wire is very important, and is usually required to be controlled within the range of ±0.01mm to ensure that there will be no problems such as poor contact or loose connection during subsequent use.
- Surface quality inspection: The surface of the copper flat wire needs to be free of scratches, bubbles and flaws. Manufacturers need to be equipped with high-precision testing equipment (such as microscopes, laser measuring instruments, etc.) to ensure surface quality.
- Mechanical properties test: Including tests such as tensile strength, yield strength, and elongation to ensure that the copper flat wire can withstand the mechanical loads in actual work.
7. Environmental protection and safety
- Waste recycling and environmental protection: Waste and exhaust gas will be generated during the production process, which must be handled in strict accordance with environmental protection standards. Manufacturers should have a complete waste recycling and treatment system to ensure that the production process does not pollute the environment.
- Safety production management: Since the production of copper flat wire involves high temperature, high pressure and chemical treatment processes, manufacturers must strictly implement safety production regulations to ensure the health and safety of workers.
in conclusion
The production of small-size copper flat wire involves multiple technical links, including precision rolling, annealing, cleaning, alloy selection, etc. Each link needs to be strictly controlled to ensure that the final product can meet high standards of electrical and mechanical properties.RaytronExperienced manufacturers such as , with years of technical accumulation and process optimization, are able to provide customers with high-quality small-size copper flat wires to meet the needs of various industries.