Due to the diverse application scenarios and precision requirements, small-sized copper strips cover a variety of specifications and production processes. Different specifications have significant differences in thickness, width, material and mechanical properties. The following is an overview of common small-sized copper strip specifications and their production processes:
Common specifications and models
model | Thickness (mm) | Width (mm) | Typical application areas |
---|---|---|---|
0.05×2 | 0.05 | 2 | Electronic connectors, terminals, batteries |
0.1×3 | 0.1 | 3 | Precision wiring harness, electrical components |
0.15×5 | 0.15 | 5 | Cable shielding, communication equipment |
0.2×4 | 0.2 | 4 | Photovoltaic welding ribbon, Transformer coil |
0.3×6 | 0.3 | 6 | Automotive wiring harness, switch terminals |
0.5×8 | 0.5 | 8 | Power busbar, track copper strip |
0.8×10 | 0.8 | 10 | High power connector |
Production process
- Raw material preparation
- Copper material requirements:Use high-purity electrolytic copper (≥99.99%) as raw material to ensure material conductivity and processability.
- Blank preparation: Copper blanks are prepared by casting or hot rolling process, and the thickness is usually 10-15mm.
- Rough rolling
- The copper blank is gradually thinned to about 3 mm through multiple rolling passes.
- Use emulsion lubrication to ensure material cooling and lubrication, the concentration is usually 2%-5%.
- Cleaning
- Degreasing and cleaning: remove the oil stains attached during the rolling process.
- Pickling: remove the oxide scale to ensure the surface of the copper strip is smooth.
- Passivation: Improve antioxidant properties and extend product storage time.
- Medium rolling
- Intermediate thickness rolling: The copper strip after rough rolling is further thinned to about 1mm.
- Process characteristics:
- Speed: 3-6m/s (adjusted according to rolling oil or emulsion).
- Control focus: plate quality and thickness uniformity.
- Finishing
- The final stage of sizing is to process the copper strip to its final thickness (e.g. 0.05 mm).
- Technical requirements:
- Control thickness tolerance within ±0.002mm.
- Fast speed (6-8m/s), using high-performance rolling oil.
- Annealing
- Purpose: Eliminate internal stress and improve the ductility and tensile properties of the copper strip.
- Process parameters: The temperature is controlled at 400℃-600℃, and the atmosphere is neutral or slightly reducing.
- Surface treatment
- Electroplating process: Tin plating, nickel plating and other treatments are carried out as required to improve corrosion resistance.
- Polishing process: ensure the copper strip surface is smooth and flawless.
- Slitting and packaging
- Striping: Cutting width according to customer needs, with accuracy controlled within ±0.01mm.
- Package:
- Moisture-proof and anti-oxidation packaging.
- Use vacuum packaging or rust-proof paper to ensure transportation and storage quality.
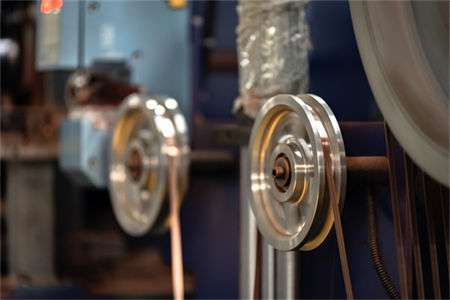
Key points for producing different specifications and models
- Ultra-thin specifications (such as 0.05×2mm)
- Technical Difficulties:It is easy to break during rolling and requires high-precision equipment and stable process control.
- Solutions: Use high-performance rolling mills (such as 20-roll rolling mills) and low-viscosity rolling oil.
- Wide specifications (such as 0.8×10mm)
- Technical Difficulties: Keep the board shape flat and the surface smooth.
- Solutions: Strengthen the control of roll pressure and plate shape in the intermediate and finishing rolling stages.
- Hardness requirements
- question: Different application scenarios have different requirements for hardness (HV value).
- Solutions: Adjust the hardness through annealing process to meet customer needs.
Ruichuang's technical advantages
- Precise control:Use high-precision rolling mills and independently developed control systems to ensure the stability of size and performance of each batch of products.
- Efficient production:Advanced medium and finishing rolling technology to achieve high efficiency and high yield production.
- quality assurance: Strict quality inspection process, surface finish, thickness tolerance and mechanical properties all meet international standards.
Summarize
Different specificationsSmall size copper stripThe production of flat copper strips needs to be optimized in many aspects such as equipment, process, raw materials, etc. to meet high quality requirements.RaytronAs a leading manufacturer of small-sized copper strips, it meets the diverse needs of customers with its professional technology and equipment, and provides stable and reliable product support for high-end manufacturing industries such as photovoltaics, electronics, and automobiles.