To produce small-sized copper sheets with good quality, precise production processes and technical requirements are required to ensure the uniformity, accuracy and stability of the materials. The following are several key points for producing small-sized copper sheets:
1. Selection and pretreatment of raw materials
Choose high-quality copper material: usually choose red copper (purity 99.9% or above) because of its excellent conductivity and ductility. Red copper is an ideal choice for making high-quality copper skin.
Annealing of copper material: Copper skin needs to be annealed before rolling to improve its plasticity and toughness, ensuring that it can be rolled multiple times without cracking. The annealing temperature and time must be controlled accurately to avoid over-annealing or under-annealing.
2. Precise rolling process
Rough rolling: During the rough rolling process, a larger copper billet (such as 15mm) is rolled to a smaller thickness (such as 3.0mm) through multiple rolling passes. The rough rolling stage requires control of pressure and speed to ensure the uniformity of the material.
Intermediate rolling: The semi-finished product of about 3.0 mm is rolled to about 1.0 mm through multiple passes, usually using emulsion or rolling oil. The control of this stage is particularly important, and the choice of oil and rolling speed will affect the surface quality of the final copper skin.
Finishing rolling: The thickness of the copper sheet is further reduced to 0.5 mm or less during the finishing rolling stage. During finishing rolling, the cooling and lubricity of the rolling oil must be carefully controlled to ensure that the surface of the copper sheet is smooth and flawless.
3. Cleaning and surface treatment
Degreasing and cleaning: There will be impurities such as oil, dust, etc. on the surface of the copper sheet after rolling, and it must be cleaned with a degreasing agent and pickled to ensure the surface is clean.
Pickling and passivation: Pickling can remove oxides on the surface of the copper skin to ensure its surface is smooth; passivation helps prevent the copper skin from re-oxidation and maintain long-term stability and corrosion resistance.
Drying treatment: The copper skin needs to be dried after cleaning to remove moisture and ensure that the surface is not damp.
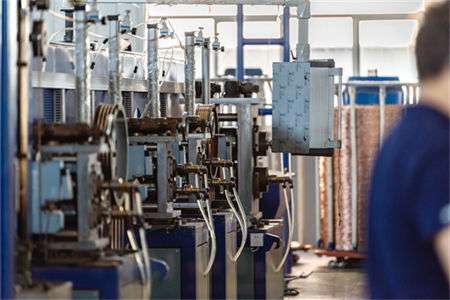
4. Precise size control
The manufacturing requirements of small-size copper sheets are extremely delicate, and size control is a crucial part of the production process. Through precision rolling mills (such as four-roller rolling mills, UC6-roller rolling mills, etc.) and high-precision measuring equipment, we ensure that each copper sheet meets strict dimensional tolerance requirements.
Thickness control: Use online measuring instruments to monitor the thickness changes of the copper skin in real time to ensure its uniformity.
Width and straightness: The width of the copper sheet needs to be precisely controlled, and the straightness and surface flatness also require strict monitoring to avoid defects such as wavy shapes and bends.
5. Environmental Control
In the production process of small-sized copper sheets, the humidity and temperature of the environment also have an important impact on product quality. Controlling the humidity and temperature of the workshop environment is the key to ensuring that the copper sheet is not damp, oxidized, or discolored.
Anti-oxidation measures: During the production process, the time that the copper sheet is exposed to air must be strictly controlled to avoid exposure to a humid environment. Before leaving the factory, the copper sheet is usually coated with a protective film or specially treated to prevent oxidation.
6. Packaging and transportation
Packaging: Small-sized copper sheets need to be properly packaged to avoid physical damage during transportation and storage. The common packaging method is to roll the copper sheet into a cylinder and wrap it with plastic film, oil paper or moisture-proof packaging material.
Transportation: During transportation, the copper sheet should be protected from severe impact and friction, and the transportation environment should be dry to avoid oxidation caused by humid air.
7. Strict quality control
Surface inspection: Use a microscope to check the copper surface to ensure there are no scratches, dirt, burrs and other defects.
Mechanical properties testing: Through tensile testing, hardness testing, etc., the tensile strength, hardness and elongation of the copper sheet are tested to ensure that it meets product requirements.
Online testing and sampling inspection: During the production process, the size, thickness and surface quality of the copper sheet are monitored in real time through online testing instruments, and regular sampling inspections are carried out to ensure that each batch of copper sheet meets the standards.
8. Technical and equipment requirements
High-precision rolling equipment: The production of small-sized copper sheets requires high-precision rolling machines, such as four-roll mills, UC6-roll mills, etc. These equipment can provide stable pressure and speed to ensure that the thickness and width of the copper sheet meet strict requirements.
Online monitoring system: Modern production lines are usually equipped with online process control systems, which can monitor the various technical parameters of the copper sheet in real time to ensure stable production and avoid deviations.
in conclusion
To produce copper sheets with small specifications and good quality, in addition to strict requirements on materials, production processes and equipment, it is also necessary to strictly control every link of production, especially in terms of size control, surface treatment, quality inspection, etc. Through refined management and technological innovation, we can ensure the production of high-quality small-size copper sheets to meet the needs of different customers.RaytronAs an industry-leading copper sheet manufacturer, we have rich technical experience and a strict quality control system, and are able to provide customers with high-quality small-size copper sheet products.