In the production process of copper-clad aluminum wire, due to the process of coating and combining two different metals (copper and aluminum), some specific technical and quality problems may be encountered. The following are several common problems in the production of copper-clad aluminum wire and their causes:
1. Poor copper layer adhesion
- Problem Description:The adhesion between the copper layer and the aluminum core is insufficient, and the copper layer is prone to peeling off.
- Cause Analysis:
- Improper surface treatment:The oxide layer on the surface of the aluminum core was not completely removed, resulting in the copper layer being unable to form a strong metallurgical bond with the aluminum.
- The coating process is not strictly controlled: Inappropriate temperature, pressure and stretching speed during the coating process may result in a loose bond between the copper layer and the aluminum core.
- Welding Problems: During the welding process of copper-clad aluminum wire, the welding temperature is too high or too low, resulting in poor contact between the copper layer and the aluminum layer.
2. Uneven copper layer thickness
- Problem Description:The copper layer thickness is uneven, resulting in unstable conductivity, and even partial thinness leads to exposed copper layer.
- Cause Analysis:
- Unstable rolling process: Improper adjustment of equipment during rolling, or uneven friction between the copper layer and the aluminum core, resulting in changes in the thickness of the copper layer.
- Uneven cooling: The copper-clad aluminum wire may not be cooled evenly after rolling, resulting in uneven shrinkage of the copper layer and thickness differences.
- Uneven material: The quality difference between copper and aluminum materials, or uneven flow occurred during the coating process of the copper layer and the aluminum core.
3. The copper clad aluminum wire is broken or pulled apart
- Problem Description: During the production process or subsequent use, the copper-clad aluminum wire breaks or breaks, affecting the performance of the product.
- Cause Analysis:
- Improper drawing process: Drawing speed is too fast or drawing temperature is too high, which can easily cause the copper clad aluminum wire to break, especially when the aluminum core is brittle.
- Alloy composition issues: Uneven quality of aluminum or alloy composition of copper layer may cause brittle fracture of copper clad aluminum wire during drawing process.
- Excessive tensile stress: During the production process of copper-clad aluminum wire, if the tensile stress exceeds the bearing range of the material, it is easy to cause breakage.
4. Copper layer oxidation
- Problem Description:The copper layer oxidizes during the manufacturing process or storage, affecting its conductivity and causing performance degradation.
- Cause Analysis:
- Humid production environment: An environment with excessive humidity may cause the copper layer to oxidize when exposed to air.
- Exposure to air during processing: If the copper-clad aluminum wire is exposed to the air during the rolling process and is not protected in time, it is prone to oxidation.
- Improper packaging: During packaging and storage, if effective anti-oxidation measures are not taken (such as using anti-oxidation film or nitrogen protection), the copper layer is susceptible to oxidation.
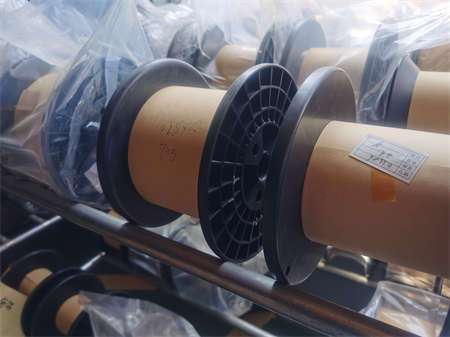
5. Surface defects of copper clad aluminum wire
- Problem Description:Scratches, cracks, pits or other physical defects appear on the surface of copper-clad aluminum wire, affecting the appearance and performance.
- Cause Analysis:
- Imprecise processing equipment: During the production process, the precision of the rolling equipment or drawing equipment is insufficient, resulting in damage to the surface of the copper-clad aluminum wire.
- Material defects:The copper or aluminum raw materials themselves have quality problems, such as defects on the surface of the material.
- Improper operation: During operation, excessive stretching or squeezingCopper clad aluminum wire, causing surface damage.
6. Copper clad aluminum wire is bent or deformed
- Problem Description: Copper clad aluminum wire is prone to bending or deformation during use, especially after long-term use.
- Cause Analysis:
- Improper control during the drawing process: Improper tension control of the copper-clad aluminum wire during the drawing process may cause stress concentration in the wire after drawing and eventually cause bending.
- Temperature control issues: During the coating process, if the temperature is not appropriate, stress concentration deformation may occur on the surface of the copper-clad aluminum wire.
- Improper storage environment: If the copper-clad aluminum wire is stored in a humid or pressurized environment, it may cause the wire to bend or deform.
7. Poor electrical conductivity
- Problem Description:The conductivity of copper-clad aluminum wire does not meet the requirements, affecting the subsequent electrical performance.
- Cause Analysis:
- Insufficient copper layer thickness:The copper layer of copper-clad aluminum wire is too thin, resulting in a decrease in its conductivity.
- Uneven coating:The copper layer is unevenly coated, the local copper layer is thin or missing, resulting in impaired conductivity.
- Quality issues of aluminum core: Poor quality or high impurity content of the aluminum core may lead to unstable conductivity, which in turn affects the performance of the entire copper-clad aluminum wire.
8. Different metal expansion rates are inconsistent
- Problem Description: Due to the different expansion coefficients of copper and aluminum, the bond between the copper layer and the aluminum core is unstable under certain temperature conditions.
- Cause Analysis:
- Inconsistent material expansion:The expansion coefficients of copper and aluminum are quite different. When the temperature changes, the expansion degrees of the two are different, which may cause cracks or separation between the copper layer and the aluminum core.
- Stress Concentration:The stress generated during heat treatment or use of copper and aluminum materials may cause the two to separate or fall off.
9. Improper temperature control during coating process
- Problem Description: During the coating process, the melting temperatures of copper and aluminum are quite different. Improper temperature control may lead to poor copper coating effect.
- Cause Analysis:
- Temperature is too high: Excessively high temperature may result in poor metallurgical bonding between the copper and aluminum layers, or even cause burning or excessive expansion of the material.
- Temperature is too low: Too low a temperature may result in insufficient bonding between copper and aluminum, forming a weak interface.
How to avoid these problems?
- Strictly control process parameters: Ensure that the process parameters (such as temperature, pressure, stretching speed, etc.) of rolling, cladding, drawing, welding, etc. are within a reasonable range.
- Improve raw material quality:Use high-quality copper and aluminum raw materials to avoid the impact of impurities in the raw materials on performance.
- Optimized surface treatment: Before coating, thoroughly clean the surface of the aluminum core, remove the oxide layer and impurities, and ensure a firm metallurgical bond between the copper layer and the aluminum.
- Strengthen quality control: Real-time monitoring is carried out during the production process to ensure that quality indicators such as size, copper layer thickness, and surface finish meet the requirements.
- Strengthen equipment maintenance and upgrades: Regularly inspect and maintain production equipment to ensure equipment stability and accuracy.
- Packaging and storage: Take effective moisture-proof and anti-oxidation measures to ensure that the quality of copper-clad aluminum wire is not affected during storage and transportation.
Through reasonable process optimization, quality control and strict testing, various problems encountered in the production process of copper-clad aluminum wire can be effectively reduced to ensure the stability and reliability of the product.