existPhotovoltaic welding ribbonIn the production process, there are indeed some common technical problems, which not only affect the production quality of the welding strip, but also affect the finalPhotovoltaic modulesThe following are common problems in production.
1. Welding ribbon bending problem
- type: Including sickle bend, S-bend, head deviation, tail deviation and other situations.
- Influence: The side bending of the welding ribbon will cause the welding ribbon to be uneven during the string welding process, which may cause the battery cell to be welded.WhiteThe phenomenon of whitening not only affects the conductivity of the solder joint, but also may affect the power generation efficiency of the photovoltaic module.
- Solutions: During the production process, the curvature of the soldering ribbon needs to be strictly controlled to ensure its flatness during rolling and transportation.
2. Tinning Problem
- type: Includes bottom layer tin plating, interlayer tin plating and top layer tin plating.
- Influence:Uneven soldering can causeHidden crackandSingle point weldingHidden cracks may lead to loose solder joints, affecting the connection stability of the battery cell; while over-soldering may cause overheating of the welding part and damage the material of the battery cell.
- Solutions: To ensure that the tin layer is evenly distributed, control the tin coating process and equipment parameters to ensure that the amount of tin in each layer of the solder strip is appropriate.
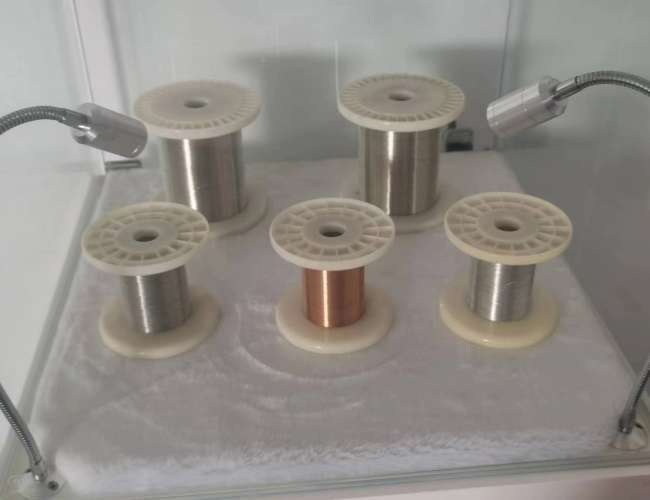
3. Yield problem
- Standard range:Usually the yield strength standard of welding strip is 60-70(Unit: MPa), although the specific standards vary depending on customer requirements.
- Influence:If the yield strength of the solder strip is too high, it may cause the solder strip to deviate during the soldering process, or even causeWhiteToo high a yield point may also cause the welding strip to lose its necessary flexibility, increasing welding difficulties.
- Solutions: The yield point needs to be strictly controlled to ensure that the welding strip can provide sufficient strength and flexibility during welding to avoid deviation and poor welding.
4. Tensile strength problem
- Standard requirements:Generally, the tensile strength of the welding strip should be greater than or equal to 185 MPa.
- Influence:If the tensile strength is too low, the welding strip may be deformed and offset during welding, which will affect the stability of the welding point and even causeWhiteAnd other phenomena.
- Solutions:Ensure that the tensile strength of the soldering ribbon meets the standard requirements to avoid quality problems caused by excessive stretching of the soldering ribbon.
5. Concentricity and tin layer issues
- Influence: An uneven tin layer, or a tin layer that is too thin or too thick, will affect the welding quality.
- Tin layer is too thin:It will affect the contact quality of welding and easily lead toCold solderingPhenomenon, that is, the soldering point is not firm and the current transmission is unstable.
- Tin layer is too thick: will causeOverflowThe phenomenon, that is, solder overflows, causes unnecessary losses and even affects the stability of the welding equipment.
- Solutions: Control the thickness and uniformity of the tin layer and maintain appropriate tin layer coverage to ensure welding quality. For the production of round solder strips, special attention should be paid to this.
Summarize
These problems that are prone to occur during the production of photovoltaic ribbons, such as ribbon bending, uneven tin plating, unqualified yield strength, insufficient tensile strength, and uneven tin layer, will directly affect the welding effect of photovoltaic modules and the electrical performance of the modules. Therefore, during the production of the ribbons, the production process must be strictly controlled to ensure the consistency of the physical and electrical properties of the ribbons, so as to ensure the stability, efficiency, and durability of the final photovoltaic modules.
Through meticulous process control and quality testing, ribbon manufacturers can ensure their products meet stringent industry standards, thereby improving the overall performance of PV panels.