The process of producing track copper strips requires high precision and meticulous control. Track copper strips are generally used in rail transportation such as railways, subways, and light rails. As conductive strips and contact strips, they have high requirements for the conductivity, wear resistance, and stability of the product. The following are the key process steps for the production of track copper strips:
1. Raw material selection
Choose high-purity, high-conductivity copper materials. Usually oxygen-free copper or red copper is used, and the impurity content is required to be extremely low to ensure excellent conductivity and ductility.
Pre-treatment of raw materials, including surface cleaning and removal of oxide layers, to avoid surface defects during subsequent processing.
2. Precision rolling
Multi-pass rolling: The thickness and width of the copper strip are controlled by a multi-pass step-by-step rolling process. Using a four-pass rolling mill or a six-pass rolling mill can achieve higher thickness uniformity.
Progressive cold rolling: The thickness is reduced less each time, and the required accuracy is gradually achieved, which can effectively avoid cracks or breaks caused by stress concentration.
Real-time thickness detection: The online laser thickness gauge monitors the thickness during the rolling process in real time and automatically adjusts the rolling pressure to ensure uniform thickness.
3. Intermediate annealing treatment
Annealing eliminates rolling stress, so that the copper strip still maintains flexibility and tensile strength after multiple rolling passes.
Annealing is performed in a protective atmosphere (such as hydrogen or nitrogen) to prevent oxidation of the copper strip surface. The temperature and time must be strictly controlled to ensure annealing uniformity.
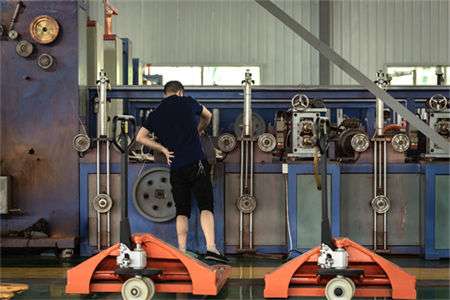
4. Precision surface treatment
Polishing: The surface of the copper strip after annealing usually needs to be polished to remove the oxide layer and impurities to ensure surface smoothness.
Anti-oxidation treatment: Commonly used plating treatment (such as tin plating, nickel plating) or special coating protection to enhance the corrosion resistance of the copper strip and increase the life of the product in a humid environment.
5. Forming and trimming
Precision slitting: Use high-precision slitting equipment to cut the copper tape into small sizes that meet specifications. The flatness and width accuracy of the cut edge are very important because it affects the laying effect of the track copper tape.
Deburring: After cutting, the copper strip needs to be deburred to ensure that the cutting edge is smooth and burr-free to prevent wear or damage to other parts during installation.
6. Final annealing (optional)
Depending on the softness requirements of the copper strip, annealing may be required at the end. The annealing temperature and time must be strictly controlled to ensure that the copper strip's flexibility meets the use requirements and is easy to bend and fix during installation.
7. Quality Inspection
Size and thickness inspection: Use high-precision laser measuring instruments or microscopes to ensure that the size and thickness tolerances of the copper strip meet the requirements.
Surface finish inspection: Check the surface of the copper strip for scratches, oxidation spots or other defects through visual and microscopic observation to ensure the smoothness.
Conductivity test: Test the key parameters of the copper strip, such as resistivity and conductivity, to ensure that the conductivity of the copper strip meets the requirements of rail transit.
8. Finished product protection and packaging
Protective packaging: To prevent oxidation and deformation, the copper tape needs to be coated with protective oil before packaging and use sealed packaging materials.
Storage conditions: Make sure the copper tape is stored in a dry, moderately conditioned environment to avoid prolonged exposure to humid air which may cause performance degradation.
Summarize
The production process of rail copper strips requires strict control in raw materials, rolling, annealing, surface treatment, cutting, quality inspection, etc. Achieving high-precision dimensional control and excellent electrical conductivity is the key to ensuring the quality of rail copper strips.