The production of copper strips from a copper strip machine is a complex process involving multiple processes and precision control to ensure the quality and performance of the product. The following are the main steps in the production of copper strips from a copper strip machine and how to ensure its quality through process control:
1. Material selection
The choice of raw materials is crucial: copper strips are usually made of brass (an alloy of copper and zinc) or pure copper, depending on the application scenario. To ensure the quality of copper strips, manufacturers need to select high-purity copper materials to avoid impurities that affect conductivity, ductility and mechanical strength.
Alloy composition control: If brass is used, the ratio of copper to zinc, as well as the addition of other trace elements, must be strictly controlled to ensure that the material has the required tensile strength, elongation and corrosion resistance.
2. Melting and Casting
Melting process: Copper and other alloying elements are melted in a set ratio. This process needs to be carried out at high temperature and impurities must be avoided. At the same time, the uniformity of the alloying elements must be maintained during melting to ensure that the material has consistent physical and mechanical properties.
Casting copper ingots: The molten copper is formed into copper ingots through the casting process. The purity and uniformity of the copper ingots will affect the subsequent rolling quality, so the temperature control, cooling speed and other process parameters in this link are particularly critical.
3. Hot rolling and cold rolling
Hot rolling process: After the copper ingot is heated, it is rolled into thinner plates through the hot rolling process. The hot rolling process requires the control of temperature and rolling speed to prevent the material from overheating and causing deformation or cracks. After hot rolling, the material has a preliminary thickness control, but the surface roughness is relatively large.
Cold rolling process: In order to further improve the precision and surface finish of the material, the copper sheet after hot rolling will be further thinned by cold rolling process. Cold rolling can not only accurately control the thickness of the copper strip, but also improve the mechanical properties of the material (such as hardness and toughness) and improve the surface quality.
4. Annealing
Heat treatment annealing: After hot rolling and cold rolling, the internal stress of the copper strip will increase, which may lead to increased brittleness or decreased mechanical properties. Therefore, annealing (heating and gradual cooling) is required to eliminate internal stress and improve the ductility and machinability of the material.
Temperature control: Accurate temperature control during annealing is very important. Too high or too low a temperature will affect the final performance of the copper strip. After proper annealing, the copper strip will become softer and have higher toughness and plasticity.
5. Surface treatment
Descaling: During the rolling and annealing process, scale may form on the surface of the copper strip, which will affect the conductivity and aesthetics of the material. Therefore, it is necessary to remove the surface oxide by pickling or other chemical treatment to ensure that the surface of the copper strip is smooth and free of defects.
Surface coating: Depending on the application requirements, the copper strip may need to be surface coated (such as tin plating, nickel plating, etc.) to enhance its corrosion resistance or conductivity. The uniformity of the surface treatment, coating thickness and adhesion all need to be strictly controlled to ensure the long-term performance of the copper strip in use.
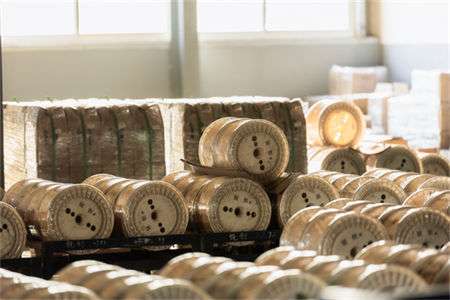
6. Precision cutting and forming
Dimension control: The width and thickness of the copper strip used in the copper strip machine must meet precise specifications. The copper strip is cut into sizes that meet customer requirements using high-precision shearing equipment. During the production process, the thickness and width of the copper strip are monitored in real time using laser or mechanical measuring tools to ensure dimensional accuracy.
Terminal forming: According to customer needs, some copper strips need to be processed into specific shapes during production to adapt to the use of terminals. During the forming process, the control of pressure and angle is very important to ensure that the copper strip can be crimped and connected to the wire smoothly and achieve the ideal strength.
7. Quality Inspection
Physical performance testing: During and after the production of copper strips, the physical properties of the copper strips need to be tested, including tensile strength, elongation, hardness and other indicators. Only copper strips that meet the standards will continue to be processed or shipped.
Surface quality inspection: The smoothness and flatness of the copper strip surface are also crucial. The copper strip surface is inspected by manual and automated equipment to ensure that there are no scratches, cracks, oxide residues and other defects to avoid affecting the appearance and performance of the product.
Electrical performance test: For copper strips used in the electrical industry, conductivity testing is also an essential step. Ensuring that the copper strips have excellent conductivity is the key to improving product quality.
8. Packaging and transportation
Protective packaging: To avoid damage to the copper strip surface during transportation and storage, the finished copper strip needs to be protected with special packaging materials to prevent it from being scratched or oxidized. It is usually wrapped with plastic film, paper rolls, etc., and moisture-proof packaging is used to prevent it from getting wet.
Labeling and classification: Packing is carried out in batches according to customer needs, and detailed labels (including product specifications, production batches, quality inspection certificates, etc.) are attached to ensure that the copper strips received by customers meet their requirements.
9. Customer feedback and continuous improvement
Tracking customer feedback: Manufacturers need to continuously track customer feedback to understand the performance of copper strips in actual use. This helps manufacturers to continuously optimize production processes and improve product quality.
Process improvement and R&D investment: During the production process, manufacturers can continuously improve the process, improve production efficiency and product stability based on feedback and their own experience. At the same time, they can increase R&D investment to develop high-performance copper strip products that better meet market demand.
Summarize
The production of high-quality copper strips for copper strip machines requires sophisticated process control and strict quality inspection. From material selection to final packaging, every link is crucial. Only by reasonably controlling the parameters of rolling, annealing, surface treatment and other links can the mechanical properties, conductivity and appearance quality of the product be guaranteed.RaytronAs a leader in the industry, with years of experience and advanced equipment, we can ensure the excellent quality of each batch of copper strips to meet various application requirements.