The production process of FPC (Flexible Printed Circuit Board) involves multiple steps, each of which is critical to the quality of the final product. The following is the general process and quality assurance measures for FPC production:
FPC production process
Design and proofing:
Use CAD software to design circuits and determine the circuit diagram, number of layers, materials, dimensions, etc.
Make a prototype for verification to ensure that the design meets the functional requirements.
Materials preparation:
Choose a suitable substrate (such as polyimide PI or polyester PET) and copper foil.
Materials must undergo rigorous testing to ensure they meet standards.
Film formation and photolithography:
The photosensitive coating is applied to the surface of the substrate to form a photosensitive layer.
Through exposure and development, a circuit pattern is formed.
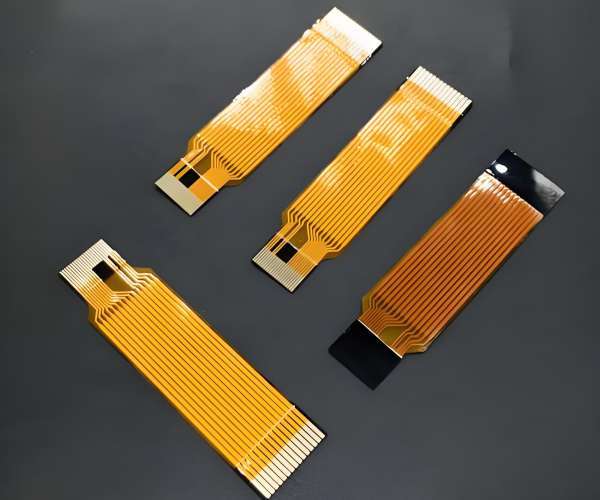
Etching:
Chemical agents are used to remove the unprotected copper to form the desired circuit pattern.
Time and temperature must be controlled during the etching process to ensure the accuracy of the circuit.
De-filming and cleaning:
Remove photosensitive coatings and clean the surface to ensure clean circuits.
Electroplating and copper plating:
The traces are electroplated to increase conductivity and thickness.
It may be necessary to add additional layers to a multi-layer circuit board.
laminated:
The multiple layers are laminated together, usually using heat pressing.
Ensure bonding strength between different layers.
Cutting and forming:
Cut to specific shapes and sizes as required.
May include punching and other processing.
Final inspection and testing:
Perform electrical tests to check continuity, insulation, etc.
Ensure that all functions are normal and meet the design requirements.
Packaging and delivery:
Qualified products are packaged to ensure safety during transportation.
Product quality assurance measures
Strict material selection:
Use high quality raw materials to ensure that the substrate and copper foil meet international standards.
Production process monitoring:
Real-time monitoring is carried out at each production link to ensure that parameters (such as temperature, time, etc.) are controlled within the standard range.
Quality inspection system:
Set up a dedicated quality control department to conduct regular product sampling and full inspections.
Use advanced testing equipment to conduct electrical performance and appearance inspections.
Staff training:
Provide professional training to employees regularly to improve their skill level and quality awareness.
ISO certification and standardization management:
Obtained ISO9001 and other quality management system certifications to ensure the standardization of the production process.
Establish a standard operating procedure (SOP) to ensure that each link has rules to follow.
Feedback and improvement mechanism:
Collect customer feedback, adjust production processes and procedures in a timely manner, and continuously improve product quality.
Through the above strict production processes and quality assurance measures, FPC manufacturers can effectively improve the reliability and stability of their products to meet market demand.